3年前,晶牛集团根据中国建筑材料联合会会长乔龙德到该集团考察时作出的关于“晶牛微晶应在水泥、玻璃两个二代的升级突破中有所作为”的指示,晶牛集团设计院集中多方力量研发出中国首创、世界领先的能够满足水泥行业特殊需要的,耐磨、耐腐、耐高温、耐冲击的“四耐”工业微晶,并成为国家标准。之后,集团迅速装备了位于华北地区的金隅、山水两大集团数百家水泥企业的预热器、篦冷机等设备。特别是在预热器5级下料管内衬的应用显示,不仅解决了高温结皮、堵塞通道等历史难题,还使下料管的外皮温度有了显著下降,为水泥生产转型升级、节能降耗迈出了可喜的第一步。
为满足数百家已应用晶牛集团产品的水泥企业新的、更高的要求,晶牛集团经过一年的创新研发,又研制出了免结皮高隔热整体节能微晶下料管。此微晶管在外皮温度下降40℃的基础上,再次下降100℃,使原管外皮温度由220℃降至80℃,并在安装施工中节省80%的工时,由原来施工安装需要10天时间缩短至两天。首批免结皮整体微晶下料管经华东地区海螺、中建材两大集团的水泥企业3个月-4个月的投产应用,均获得了理想成果。
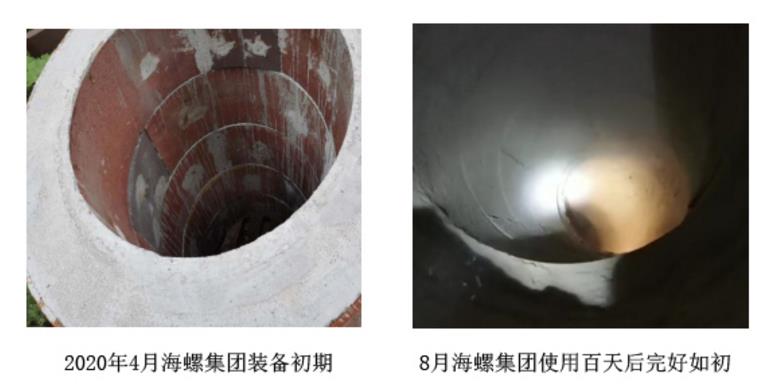
海螺、中建材两大集团企业生产部技术人员提供现场数据的显示,不仅下料管温度下降百余度,且整体管配有中国首创航天微晶玻璃装备的高温观察窗。不必打开原金属密封门窗,不会使管内高温负压吸入外部冷空气而导致生产工艺波动。内衬不再结皮,不必放炮崩渣,也不必人工清理结皮,大大压缩了操作工艺。依据百家水泥企业的应用效果,按每条日产5000吨水泥生产线计算,若下料管、烟室、分解炉、旋风筒、鹅颈管等预热器的外皮温度都能下降百余摄氏度,不仅稳定工艺、提高了产量与质量,而且免去放空气炮的设备能耗成本,清结皮的人工成本及每年都有的堵塞停产事故、人身烧伤事故造成的损失,综合年节能、增产、降耗的经济效益将达千万元。这使“四耐”微晶在水泥行业的转型升级中再显异能、再攀高峰。
中国建材报网记者 会杰 晶洁 永生
|